효능이 입증된 원료의약품이 완제의약품으로 가공되어 환자에게 적용되기 위해서는, 원료의약품의 효능을 최대한 유지하면서 안전성이 보장되는 공정의 확립이 필수적입니다.
공정이란 원료의약품의 제조, 분리, 정제, 포장 등의 과정을 포함하며, 의약품은 일정한 기준의 품질과 안전성을 충족하면서 환자에게서 최대한의 약효를 나타내야 하기 때문에 이를 만족하기 위한 공정의 개발과 꾸준한 개선은 제약사의 경쟁력이라고 할 수 있습니다. 공정 설계와 최적화 과정의 가장 최신 개념인 설계기반 품질고도화 (Quality by Design, QbD)에 대해서 알아보겠습니다.
QbD란?
QbD는 기존 제약 산업에서 이원화되어 있던 제약 공정과 품질 시험 단계를 일원화함으로써 생산 효율의 극대화와 품질의 고도화에 목적을 두는 시스템입니다. 지속적인 분석과 결과에 대한 피드백을 통해 최적화된 공정을 설계하며, 제약사에는 효율성을, 환자에게는 효능과 안전성을 보장하는 전략적 프로세스라고 할 수 있습니다.
QbD의 실행 단계
QbD는 국제조화회의(International Conference on Harmonization, ICH)의 품질 가이드라인 중, Q8, Q9, Q10을 참고하여 설정된 6단계로 나누어집니다. 원료의약품에 대한 선행 지식을 기반으로 공정이 원료에 미치는 영향을 고려한 설계 방식으로, 효율적이고 반복적인 개선이 가능한 점이 특징입니다.
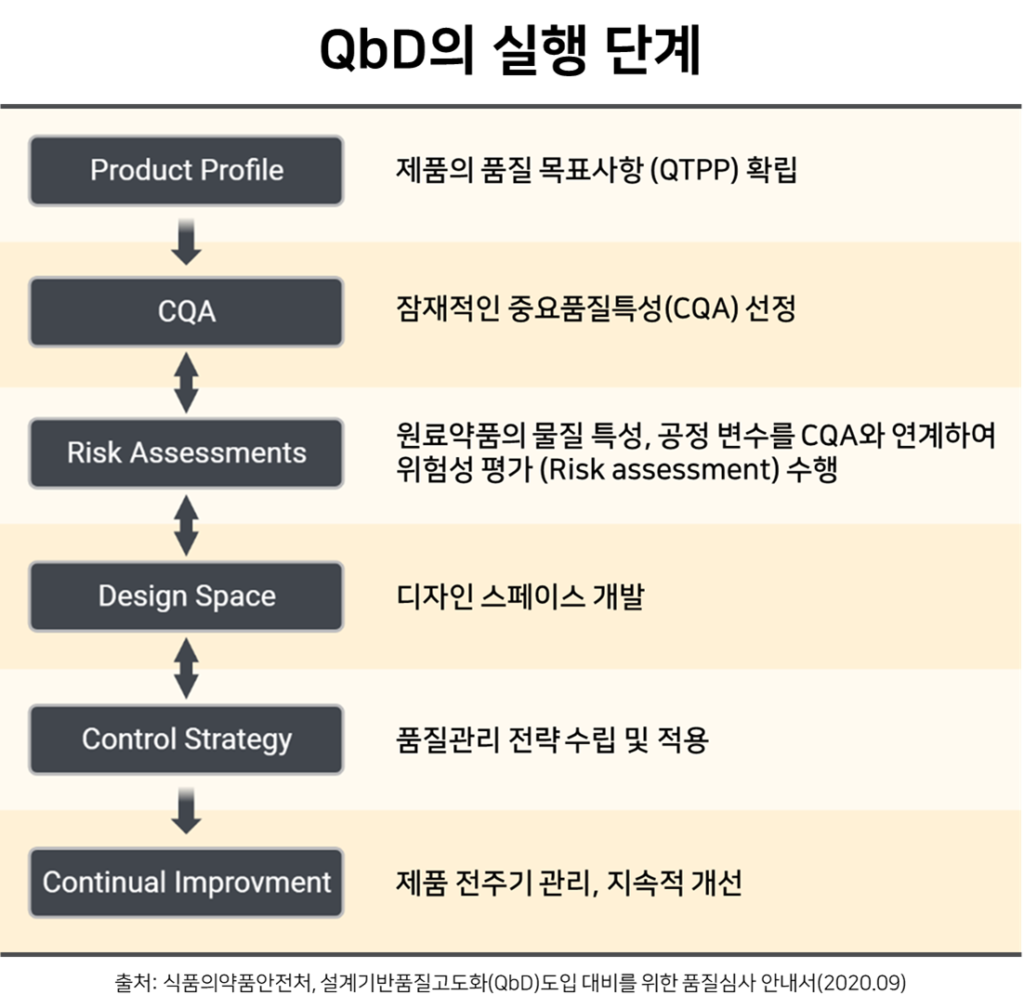
QbD의 장점
이전의 공정 개발법은 공정 변수들이 고정적이며, 동시에 다양한 변수들을 고려한 연구개발이 불가능했습니다. 실험적 분석법이 아닌 경험적인 데이터들에 의존하여 공정이 개발되었으며, 제약 공정과 품질 시험 단계의 분리로 공정의 개선이 번거로웠다는 단점이 있었습니다.
그러나 QbD의 경우 과학적/통계적 데이터를 기반으로 한 디자인 스페이스 구축을 통해 다량의 변수들을 일시에 고려한 공정의 연구개발이 가능했고, 공정 변수들에 대하여 유연한 조절이 가능하다는 것이 큰 장점입니다. 또한 반복적인 피드백으로 공정의 최적화가 이루어지는 시스템으로, 차질 없는 체계적인 공정 개선이 이루어질 수 있어 고순도, 고효율의 완제의약품 공정 개발을 위한 최선의 전략으로 기대하고 있습니다.